How to Minimize Downtime in Manufacturing: Best Practices and Strategies
Posted By - Pony
Posted On - July 24, 2023
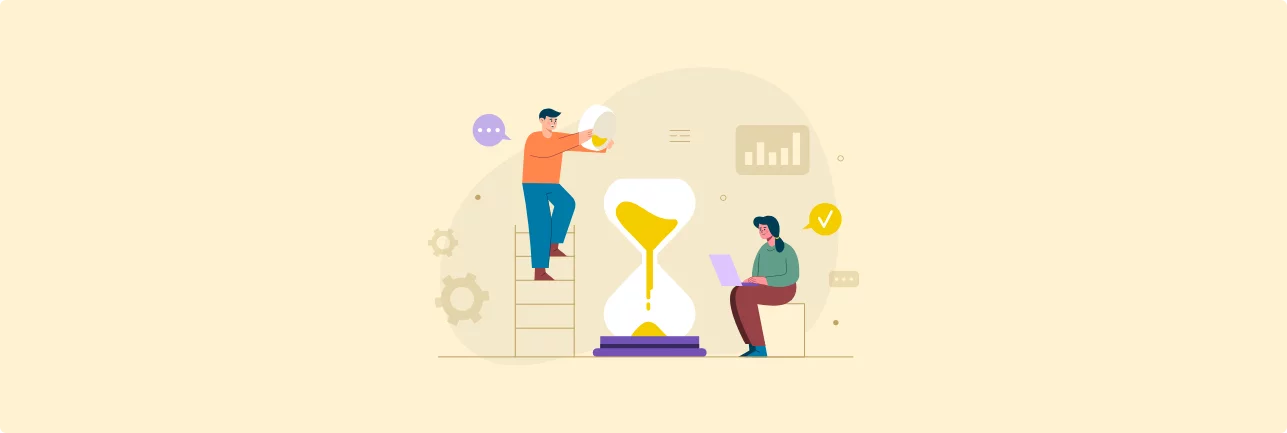
As a business owner, you are careful about losing every dollar. But did you ever check how much it costs you if there is an asset failure or a production loss due to natural or man-made incidents? This actually refers to downtime which means your output gets stopped. May it be a planned downtime or an unplanned downtime, you will lose big bucks. To shield your downtime this blog will teach you some practices from the perspective of a Manufacturing application development company
These practices are effective ones to minimize downtime. So, let’s not waste time and start.
While thinking about downtime, the first thing that will come to your mind after reading the introduction is planned and unplanned downtime. Here’s the answer for you.
What is Planned and Unplanned Downtime?
Sometimes you stop your production for asset maintenance. When a production halt is predicted and not influenced by any unforeseen event, the downtime is called planned downtime. On the reverse side, there is unplanned downtime. Unplanned downtime is the time period when your production stops because of some unforeseen events like IT asset failure, human errors or sudden breakdown of machinery.
Hope, now you can differentiate between the two. If you are fed up with downtime, then follow the below strategies to minimize them.
1. Process Automation
To reduce unexpected downtime especially caused by human errors, the best solution is to automate your manufacturing business process. When downtime is affecting your business efficiency, get equipped with process automation. Process automation is done by a manufacturing application development company. So, go harness the process automation solution and reduce your downtime.
2. Real-Time Data and Analytics
Monitoring the production process gives a way to reduce downtime. In today’s data-driven world, real-time data and analytics can help you to check your production continuously. This is another strategy to reduce downtime. Real-time data and analytics is a process that integrates IoT devices and other data-capturing tools into your manufacturing machinery and process. The data is processed through metrics and bottlenecks if any on the production floor are identified.
3. Tailored Solutions
Getting done with a tailored solution can help to reduce downtime. A manufacturing application development company gives you a tailored software solution. When you approach the software company with your production challenges, they provide you with custom software that can identify potential production failures before they occur. Hence you can stay safeguarded against any breakdowns.
4. IT Training of Employees
Training makes your manpower more efficient. Software tools given by a manufacturing application development company can then only be handled properly if you give proper IT training to your production managers. When you provide IT training, your production managers become efficient to manage and monitor production data through intelligent gadgets. And you will not face any unexpected downtime that hurts you more.
Finishing off
When your manufacturing unit has adopted each and every IT solution of a manufacturing application development company, your IT teams and production team are front-line forces to address downtime. Expected downtime is accounted for but especially the unexpected ones can be reduced by employee IT training, process automation, tailored solutions, and real-time data analytics. So, put your manufacturing profits in your pockets once again by reducing downtime through software solutions.