Predictive Maintenance: Enhancing Equipment Reliability using Data Science
Posted By - Pony
Posted On - August 7, 2023
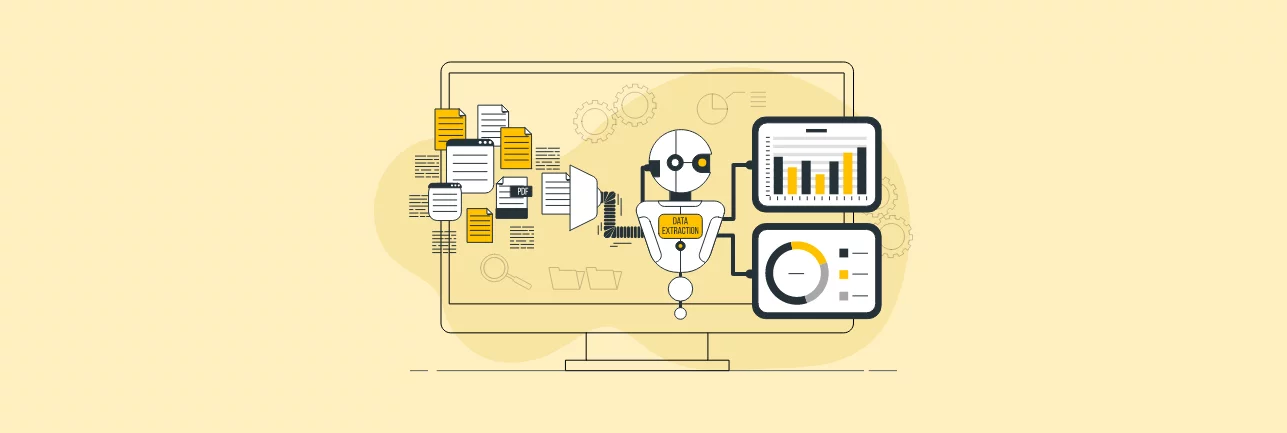
Production delays, escalated maintenance costs, and potential safety hazards pose significant challenges for manufacturers. Though these challenges exist, the manufacturing industry has discovered a game-changer: predictive maintenance, fueled by cutting-edge data science and big data analytics. With this innovative approach, industries are now proactively tackling equipment failures, ensuring uninterrupted production processes, and elevating equipment reliability to unprecedented heights. This blog delves into the significance of predictive maintenance, shedding light on how data science is spearheading a revolution in the manufacturing sector.
Here our discussion begins.
What is Predictive Maintenance?
Predictive maintenance is a data-driven approach that utilizes advanced analytics and machine learning algorithms to predict equipment failures before they happen. Traditional maintenance strategies often involve scheduled maintenance routines or reacting to breakdowns, which can be costly and inefficient. However, predictive maintenance takes a proactive approach, utilizing real-time data from sensors and machines to identify patterns and indicators of potential failures.
Role of Data Science in Predictive Maintenance
At the heart of predictive maintenance lies data science, which plays a vital role in extracting meaningful insights from vast amounts of data. Manufacturers are now integrating smart sensors and IoT devices into their equipment, collecting data on various parameters like temperature, vibration, pressure, and more. This continuous flow of data is then analyzed using big data analytics, to detect anomalies and patterns that could signify impending equipment issues.
By employing machine learning algorithms, data scientists can build predictive models that learn from historical data and predict future failures. These models enable manufacturers to schedule maintenance activities more effectively, preventing unplanned downtime and optimizing equipment performance.
5 Benefits of Predictive Maintenance
Increased Equipment Reliability
Predictive maintenance allows manufacturers to address potential issues proactively, reducing the risk of unexpected breakdowns and increasing overall equipment reliability.
Cost Savings
By identifying problems early on, manufacturers can avoid costly repairs and prevent production delays, leading to substantial cost savings in the long run.
Improved Safety
Equipment failures can pose safety risks to personnel and the surrounding environment. Predictive maintenance helps in identifying safety-critical issues before they escalate.
Enhanced Productivity
With reduced downtime and optimized maintenance schedules, manufacturers can ensure continuous production, thereby enhancing productivity.
Data-Driven Decision Making
In the manufacturing industry, data-driven decision-making is becoming the cornerstone of success. Thanks to big data analytics, manufacturers can gain valuable insights into equipment performance and overall operations. Analyzing historical data allows them to spot recurring patterns, uncover inefficiencies, and fine-tune processes for better outcomes.
To achieve data-driven success, manufacturers must ensure they have robust data infrastructure, including data collection mechanisms, storage systems, and analytical tools. Hiring skilled data scientists and engineers is essential for translating data into actionable insights and building reliable predictive models.
Challenges and Considerations
While predictive maintenance offers numerous advantages, implementing it can pose some challenges. Integrating sensor technology into existing equipment, managing large volumes of data, and upskilling the workforce to handle data-driven processes are some common hurdles. Manufacturers should also prioritize data security and privacy, as sensitive operational data is involved in predictive maintenance strategies. Implementing measures to safeguard data from unauthorized access and cyber threats is crucial for maintaining the integrity of the system.
Take away points
Predictive maintenance powered by data science is transforming the manufacturing industry, providing a proactive approach to equipment reliability and efficiency. By leveraging big data analytics, Australia manufacturers can harness the power of data to predict and prevent equipment failures, ultimately leading to increased productivity, reduced costs, and improved safety.
The manufacturing industry’s future lies in embracing data-driven strategies, where predictive maintenance takes centre stage, ensuring smooth operations and seamless production processes. As technology continues to advance, manufacturers who adopt predictive maintenance will gain a competitive edge and establish themselves as industry leaders.